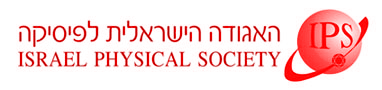
Home
About/Contact
Newsletters
Events/Seminars
2020 IPS Conference
Study Materials
Corporate Members
Home
About/Contact
Newsletters
Events/Seminars
2020 IPS Conference
Study Materials
Corporate Members
The additive manufacturing (AM) powder bed based processes utilizing selective laser melting (SLM) and electron beam melting (EBM) are growing concepts for fabrication of metal components. The main advantage in these methods is the ability to follow 3D computer designed models for layer-by-layer fabrication of complex metal products, which are impossible to achieve by conventional processing. In this study, a characterization of the microstructure and texture of Ti-6Al-4V alloy AM samples is presented. This lightweight metallic alloy offers high structural efficiency, good fatigue and creep strength and therefore, widely used in aircraft and aerospace industries. The Rietveld analysis of our neutron diffraction measurements (carried out HIPPO, LANL) show that the room temperature post-process α-phase texture is weak (up to ~ 4 times random), independent of the AM process, machine or growth direction of the sample. In most cases the reminant β-phase amount is low (less than 1wt%) and that the texture inheritance between the two Ti-6Al-4V phases is rather dull.